The gap in the development trend of spunlace nonwovens production equipment between my country and foreign countries
The gap in the development trend of spunlace nonwovens
production equipment between my country and foreign countries
At present, the newly launched spunlace production lines in my
country are mainly domestic production lines, accounting for about 80% of the
total production lines. The reason is that the price of domestic production
lines is relatively low, only 1/4~1/5 of that of imported production lines. But
it must be pointed out that the gap between the domestic line and the imported
line is also very obvious. The gap is mainly manifested in the following two
aspects:
(1) The production capacity of each production line is only
1/2~1/3 of the imported production line.
(2) There are obvious gaps in product quality regardless of
appearance quality and internal quality. The appearance of the spunlace fabric produced by the domestic production line is not as smooth and fine as that
produced by the imported production line, and the internal quality is not as
good as that of the imported production line in terms of strength and
uniformity.
In the production of medical and sanitary products, the products produced by domestic equipment are also inferior to those produced by imported equipment.
We will focus on analyzing the development trend of foreign spunlace production lines and the gaps in my country's equipment, hoping that my country's equipment manufacturers can catch up as soon as possible.
What needs to be explained here is the spunlace production line, which is not limited to the spunlace equipment itself, but also includes the front equipment opener, carding machine, web lapper, drafting machine, etc. Due to the low speed or quality problems of the front equipment, it will also affect the production efficiency and quality level of the entire production line.
The following will make some analysis on several main equipment
in the spunlace production line:
1. The development trend of front equipment and the gap between
my country and China (carding machine)
my country is a big textile country, and the production of
cotton spinning and wool spinning carding machines has a long history. Although
there are gaps in the quality and production speed of these equipment with
foreign countries, the difference is generally not much. The difference in
quality and speed of nonwoven cards is much greater. The reason is that the
biggest difference between the two is that the output products of the cotton
and wool spinning carding machines are in the form of strips, while the output
products of the non-woven carding machines are in the form of nets.
Since the manufacturers of carding machines in our country used to produce fiber products in the form of strips in the past (especially several companies that originally produced wool carding machines), they did not pay enough attention to the characteristics of net products, did not study deeply, and ignored Measures should be taken accordingly. Therefore, although the structure of carding components is generally similar to that of foreign countries, there is a big gap with imported equipment in terms of operating speed and final product quality.
What is the difference between strip output and mesh output?
First, the output is in strip form, the fibers are condensed together with high strength, the fiber strips are not easy to float up during operation, and the accidental deformation is small, and it is easier to obtain good results at higher operating speeds. However, the output of mesh products is easily affected by external interference, such as the influence of airflow and the smoothness of the conveying curtain, which may easily cause incomplete transfer, floating nets, and mutual adhesion, resulting in unexpected unevenness, and even serious entangled with each other. The higher the operating speed, the more serious this phenomenon will be.
Second, when the strip-shaped output is formed into strips, the horizontal network segments play a role in merging with each other, and the horizontal unevenness is not easy to be exposed, while the mesh-shaped output does not produce a merging effect after forming a network, so the quality of the network is higher. .
Foreign carding machines have done a lot of work to solve the problem of mesh output without floating nets, sticking to each other, and maintaining horizontal uniformity. We should learn from and learn from this aspect.
2. Cross-lapper
There are certain requirements for the vertical and horizontal strength ratio, and products with a heavier grammage must pass through a cross-lapper and a drafting machine after the carding machine. There are three major disadvantages of the traditional cross auxiliary network machine:
(1) Due to the tension of the fiber web, the fiber web produces lateral shrinkage;
(2) When the laying trolley changes direction, due to the existence of a dead point (the laying speed is 0), there is a difference between the output of the carding machine at a constant speed, and overfeeding occurs at the edge of the fiber web, resulting in the weight of the side web greater than the middle.
(3) During the subsequent consolidation, the product shrinks further in the lateral direction, which makes the problem of bias on both sides more prominent. In order to solve this problem, several major manufacturers of cross-lappers in the world have taken measures. Now, the equipment of Asselin (belonging to NSC Group) and Autefa (belonging to Dilo Group) are used to illustrate.
3. There are two main spunlace equipments in the world: Rieter perfojet and Fleissner. Its main features are stable product quality, low energy consumption, and high production capacity of each production line. In terms of production capacity, the annual output of each production line can be as high as 10,000 tons, and the annual output of a single carding machine can reach 3,000 tons/year. The domestic production line is only 800~1400t/year, which is quite different. The energy consumption of imported production lines has been significantly reduced in recent years. For example, take perfojet as an example. Before 1996, the company consumed 1 kilowatt-hour of electricity to produce 1kg of spunlace fabric. Launched JetLace-2000 after 1996, the energy consumption per kilogram of spunlace fabric has been reduced to 0.13 degrees, and now it has dropped to 0.107 degrees (both based on 30g/m 2 spunlace cloth), which is only 1/2 of that before 1996 15~1/20. Product quality has also improved significantly. The surface quality of spunlace cloth produced by foreign equipment is also significantly better than that produced by domestic equipment.
The design of the spunlace head is even more important. Practice has proved that: the strengthened design of the water thorn head prevents turbulent flow in the inner cavity of the water thorn head, ensures that the water flow is evenly distributed in the cavity, and can process products of the same grammage with lower water pressure, which can greatly reduce energy consumption and Keeps good detangling effect.
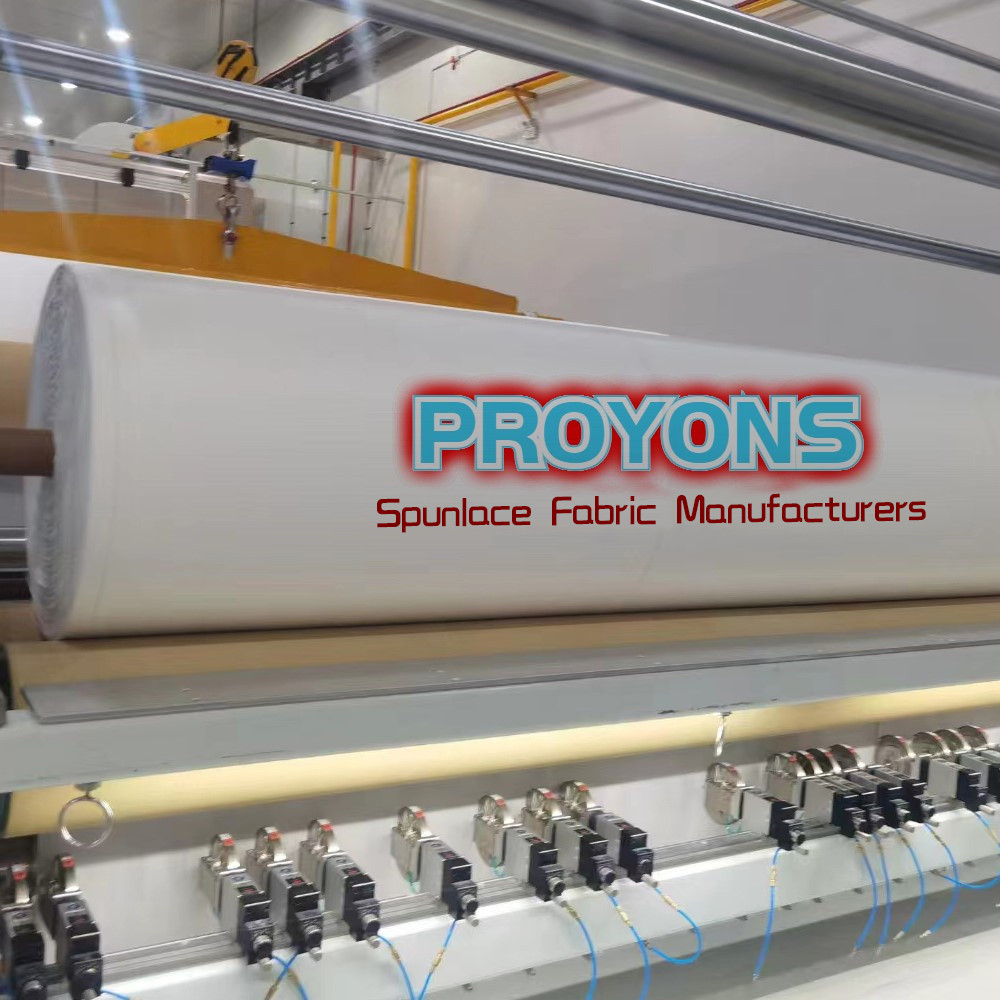